

The Ishikawa/fish-bone diagram is not suitable to solve multiple problems in one fish-bone diagram template.
#ISHIKAWA DIAGRAM MACHINE VS MATERIAL DOWNLOAD#
Thermoforming-Process-Audit-Checklist-1 Download Types of Fishbone diagram:īelow specified fish-bone diagrams can be used depending on the type of business process or product/services type.
#ISHIKAWA DIAGRAM MACHINE VS MATERIAL FREE#
This template is absolutely free to download. This template helps you to draft a root cause specific to man, method, material, machine, measurement, and environment. Please do refer attached 5M-1E/Fishbone template. For example, in 5M-1E, ‘machine’ can be replaced with ‘maintenance’. Note: If the measurement parameter not applicable for solving a problem, add the management parameter in the fishbone diagram.įishbone / Ishikawa diagram can be customized based on industry requirements. Refer to the example of the cause and effect diagram. The following specifications related to 5M-1E can be considered during brainstorming. A brainstorming always is effective if it’s lead by a leadership/management team member.įISH BONE DIAGRAM / CAUSE & EFFECT DIAGRAM Invite all relevant stakeholders for the brainstorming session. If it’s not feasible, you can still conduct a brainstorming session in a meeting room with all the required data and resources. Brainstorming: It’s better to conduct a brainstorming session on-shop floor or the place where the problem/defect is identified. Effective team management is required for better coordination between cross-functional team members and successful implementation of the fishbone diagram.ģ. For example, a process designer who deployed a business/manufacturing process can add input to build a better fish-bone diagram. Subject matter experts can add lots of value to the problem-solving process. It’s better to identify team members who are familiar with the manufacturing/business process.
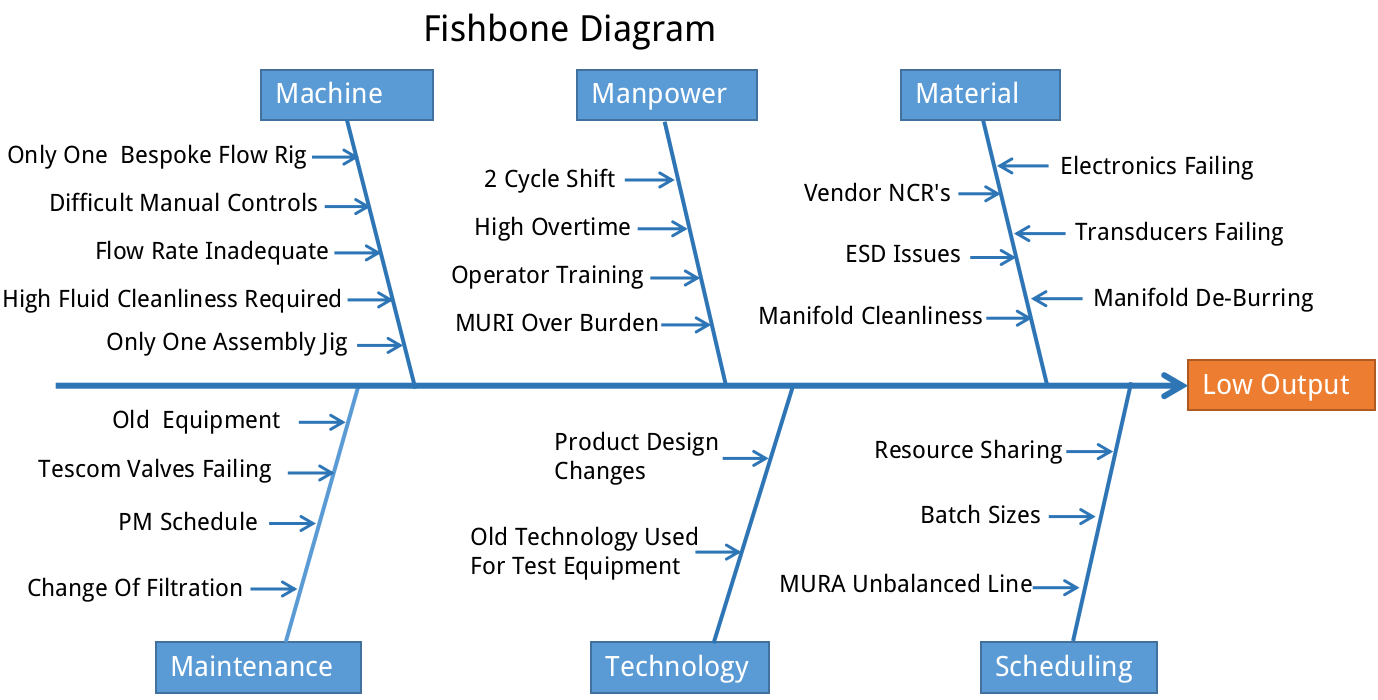
Team formation: This is a very important step for the selection of the right team member for problem-solving.
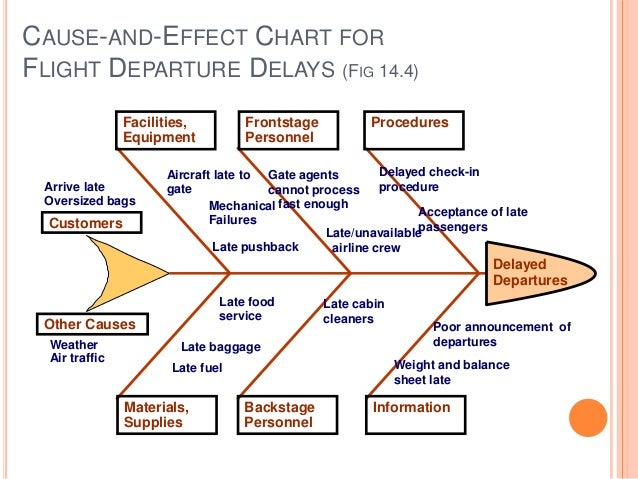
Cause-and-effect diagrams can reveal key relationships among various variables, and the possible causes provide additional insight into process behavior.How to draft a fishbone / Ishikawa diagram? It is known as a fishbone diagram because of its shape, similar to the side view of a fish skeleton.Ĭauses in the diagram are often based on a certain set of causes, such as the 6 M's, described below. It was first used in the 1960s, and is considered one of the seven basic tools of quality management, along with the histogram, Pareto chart, check sheet, control chart, flowchart, and scatter diagram. Ishikawa diagrams were proposed by Kaoru ishikawa in the 1960s, who pioneered quality management processes in the Kawasaki shipyards, and in the process became one of the founding fathers of modern management. Ishikawa diagrams (also called fishbone diagrams, or herringbone diagrams, cause-and-effect diagrams, or Fishikawa) are causal diagrams that show the causes of a certain event - created by Kaoru Ishikawa (1990), was a Japanese university professor and influential quality management.Ī common use of the Ishikawa diagram is in product design, to identify potential factors causing an overall effect and to help identify the root cause of non-conformances.
